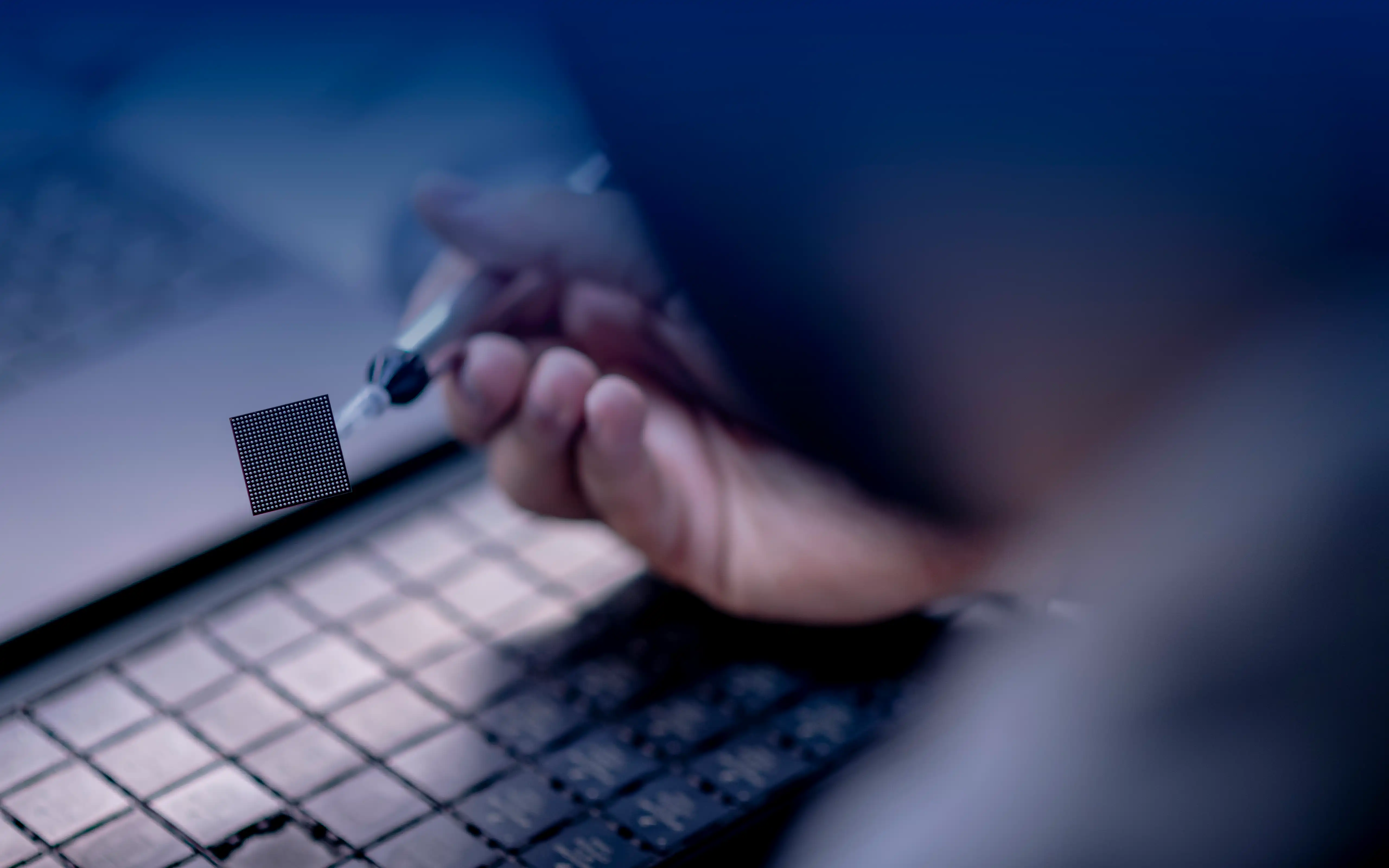
QUALITY
CONTROLLED AREA
ROOM CONTROL BY TEMPERATURE AND RH (Relative Humidity)
With today's systems, qualified personnel and transparency in all procedures, we can guarantee the necessary satisfaction and requirements.
We recognise that a good system of records is essential to achieving the highest levels of customer satisfaction. Growing in this area makes us more versatile.
All these features, along with three warehouses and a temperature and RH controlled (Relative Humidity) room, are an added value for the company to maintain a high standard and comply with established regulations.

The use of appropriate clothing is essential when entering rooms with ESD monitoring equipment, temperature and humidity equipment, filtration systems and SAS pass-through equipment to ensure the correct transfer of parts.
We then carry out a series of internal processes that are essential to the definition of our philosophy, such as visual checks using powerful microscopes, preventive and careful handling of each component, originality checks, image comparisons, solvent resistance tests, final checks... and external processes such as solderability tests and component checks using X-rays.
The development of such protocols helps us to evolve and improve our performance and demonstrate high levels of service quality. All under ISO 9001 and EN 9120 certification to ensure a seamless experience.
Our Commitments
QUALITY RELATED TO THE PROCESS OF INSPECTION AND MAINTENANCE OF COMPONENTS
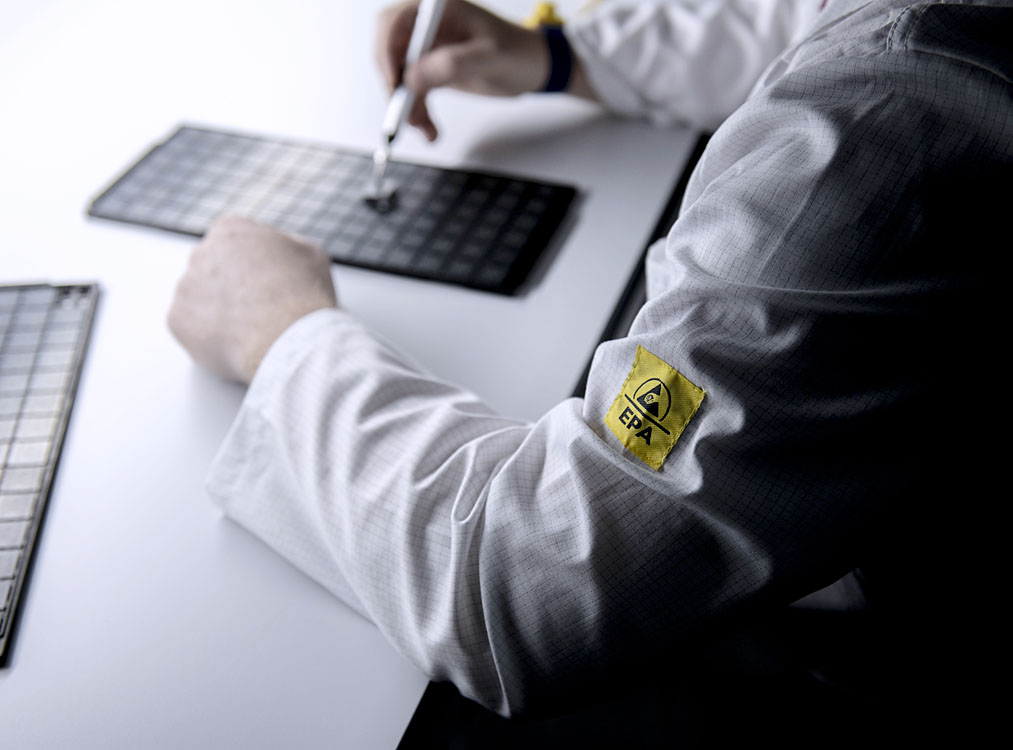
ACCESS CLOTHING
Appropriate clothing for EPA areas prevents electrostatic damage to sensitive equipment.
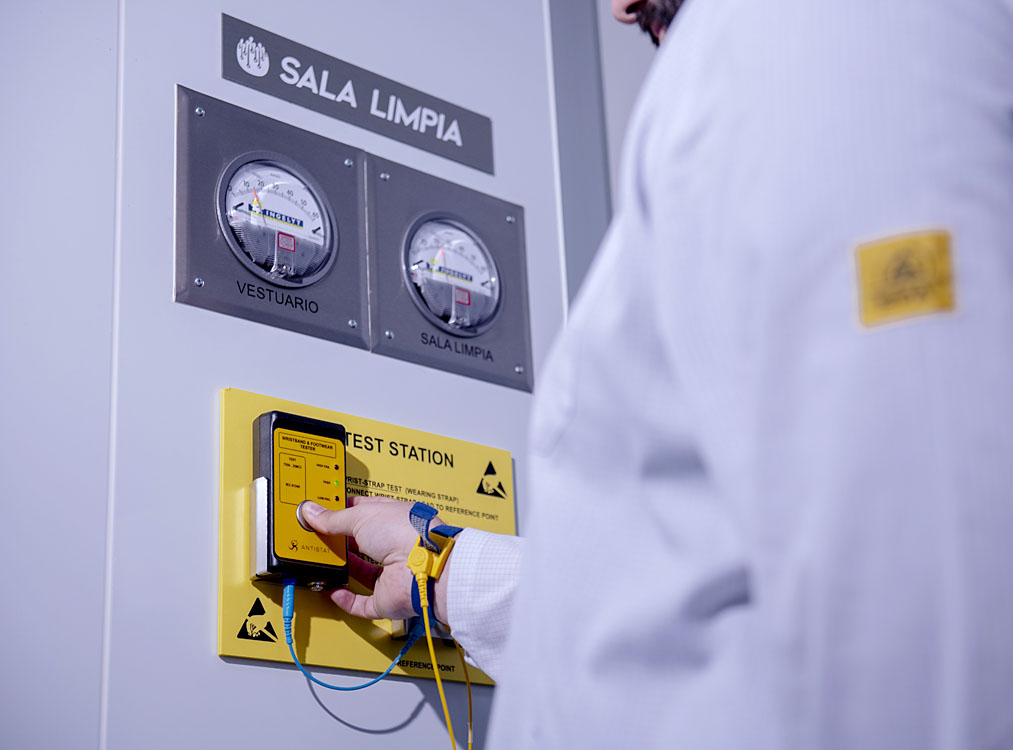
ESD CONTROLS
Check the level of electrostatic discharge by combining appropriate wristbands, footwear and gowns.
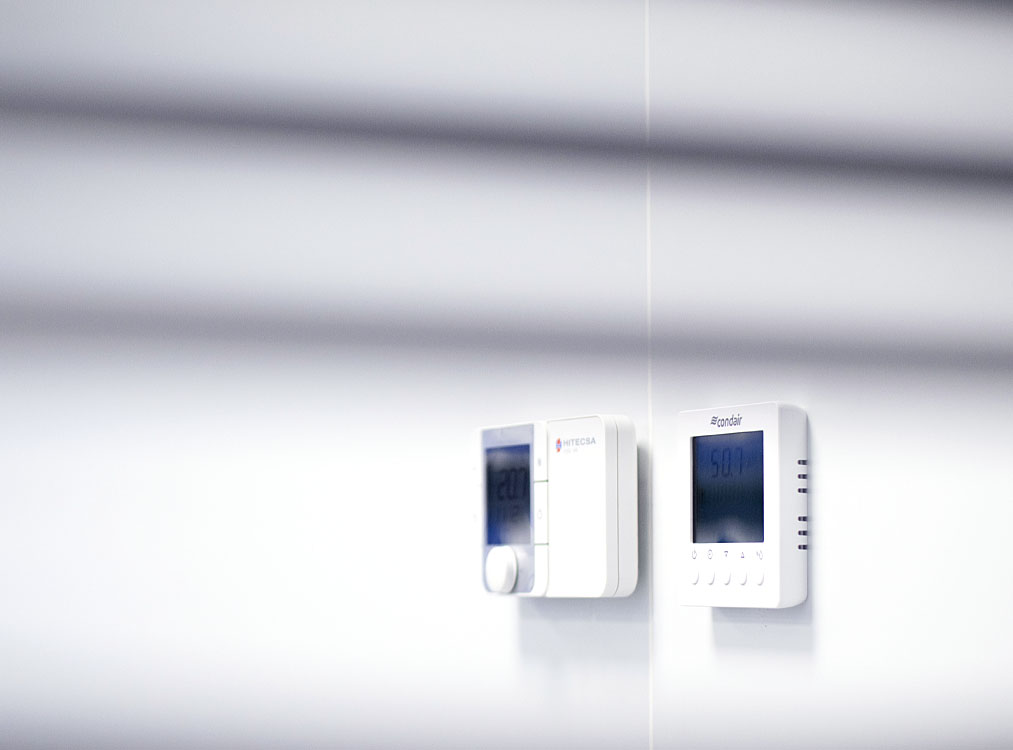
TEMPERATURE AND HUMIDITY
Climate control and humidification are responsible for the proper preservation of the material.
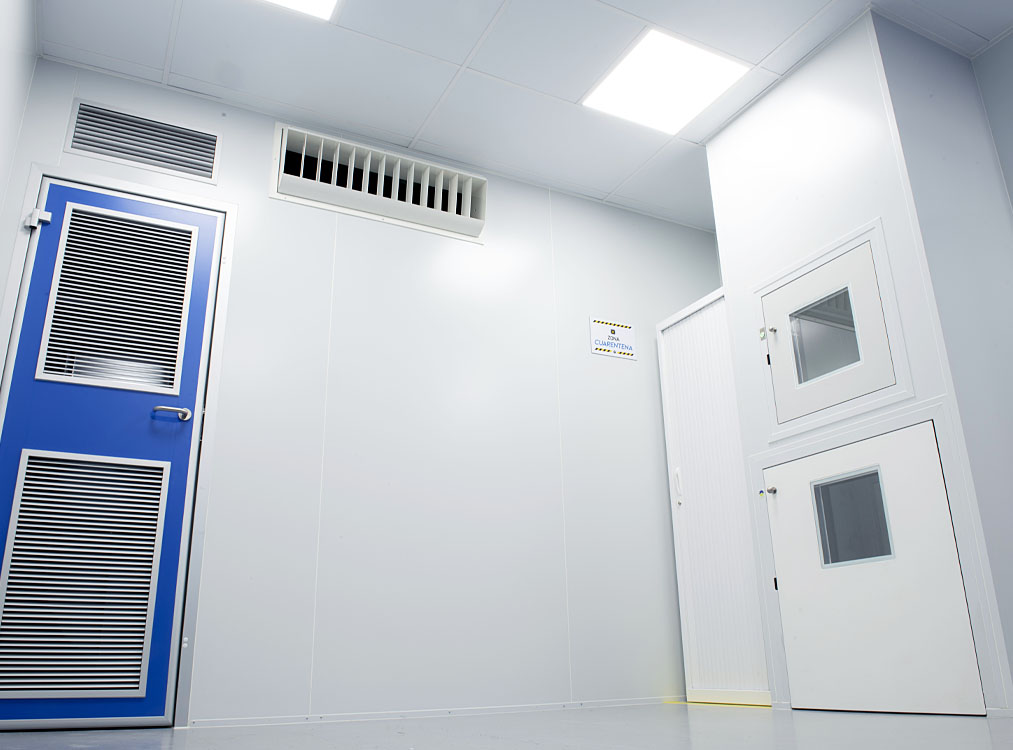
SAS PASS THROUGH BOXES
With simultaneous door-opening locking mechanisms, they ensure the transfer of objects.
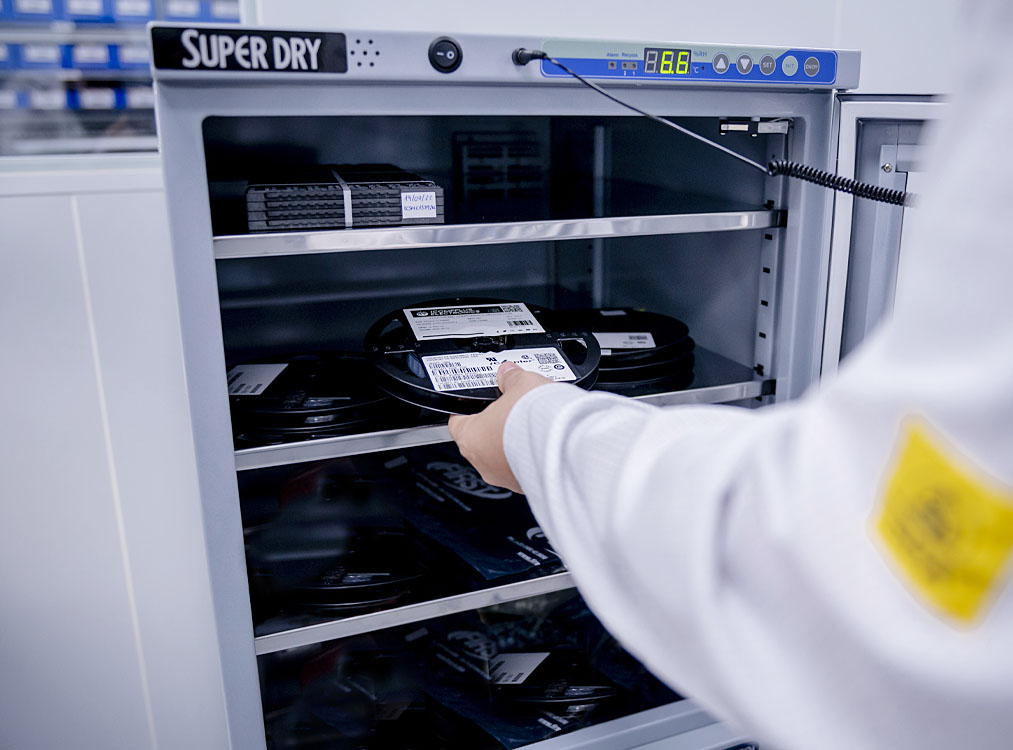
DRYING CABINS
Advanced design with ESD coating, built-in ventilation and non-stop drying.
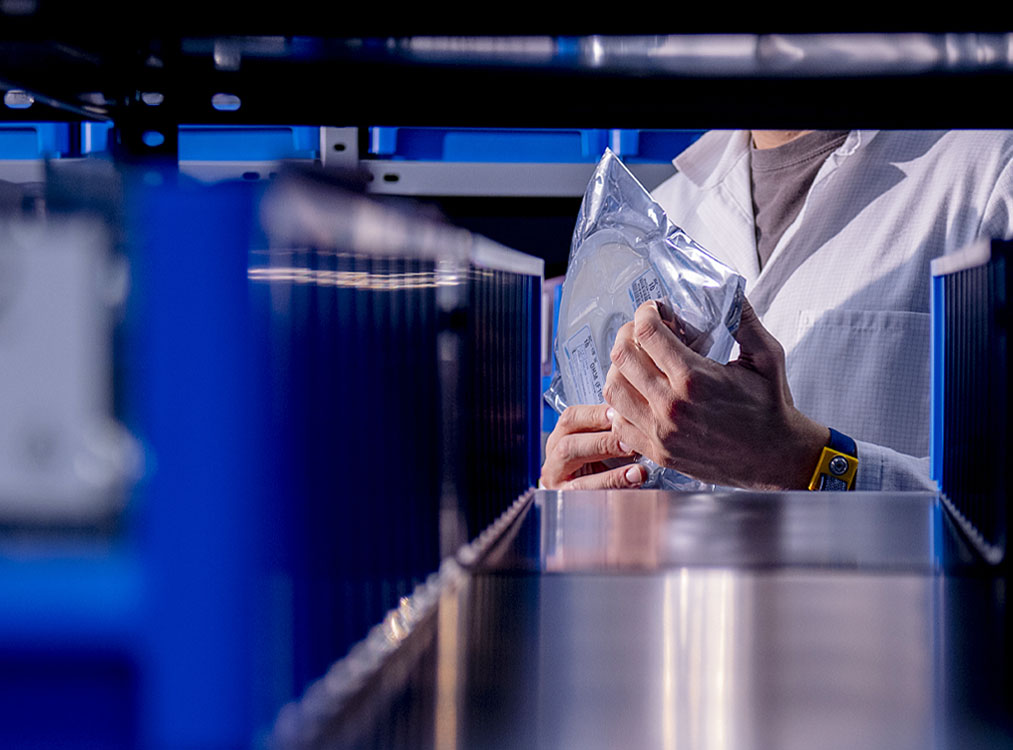
ANTISTATIC PACKAGING
Stored in antistatic materials for complete, reliable and long-lasting preservation.
INTERNAL PROCESSES
EXTERNAL PROCESSES
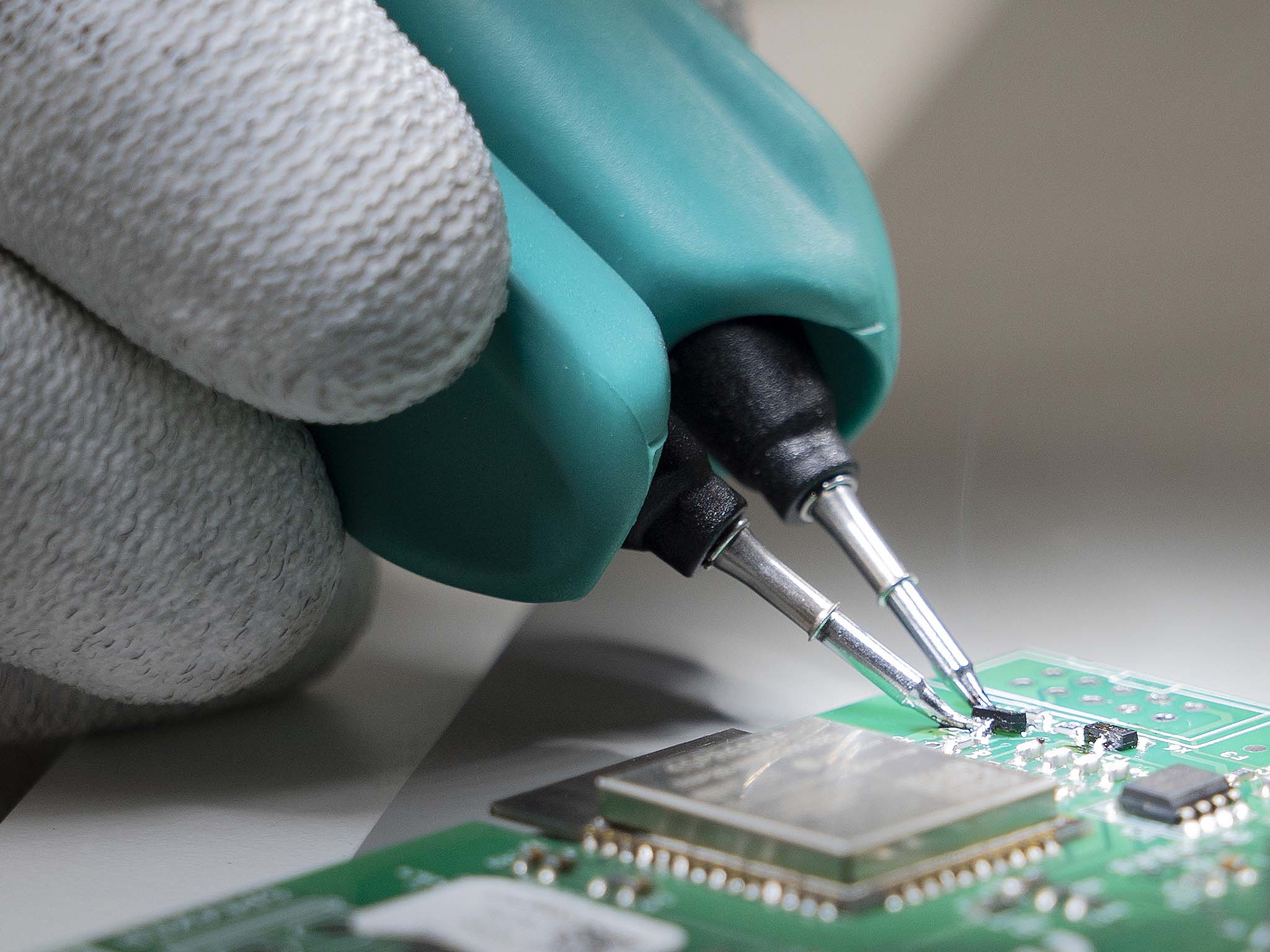
SOLDERABILITY TEST
external companies, accurate weldability tests are carried out to determine the weldability of surfaces to be joined to another surface.
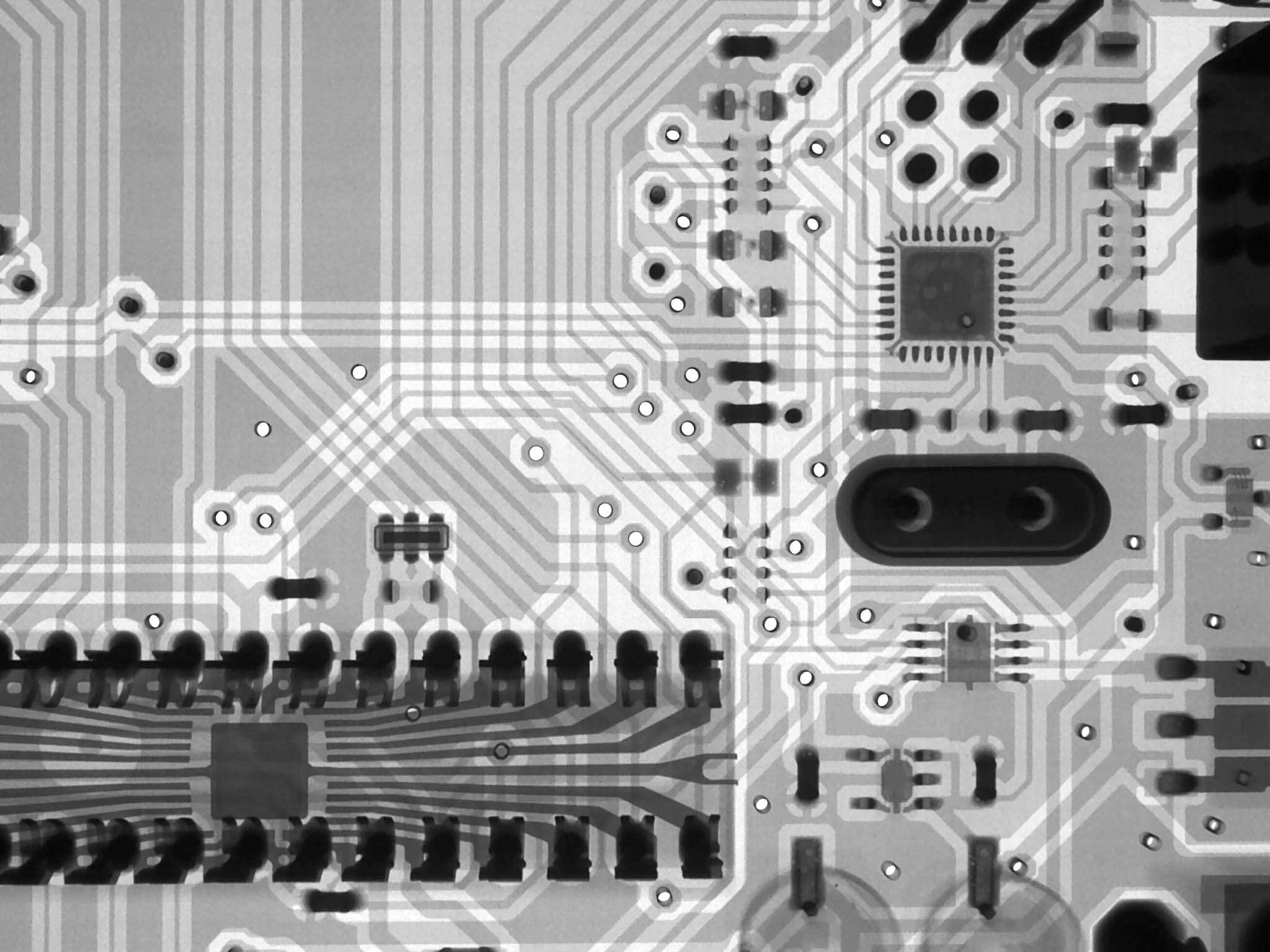
X-RAY INSPECTION
X-ray detection of defects and flaws in the internal layers of the component, which are not visible in the process, thanks to major companies with advanced systems in this field.